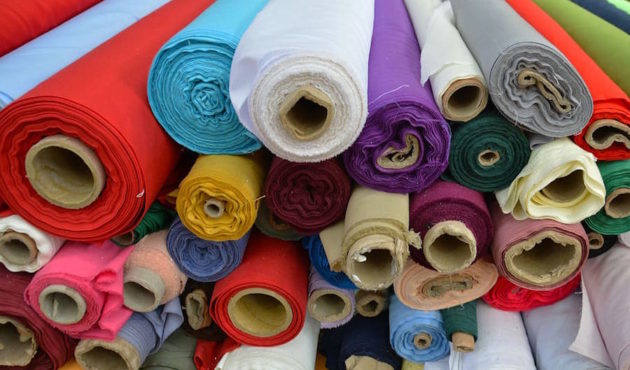
Despite the recent economic boom, the US manufacturing industry remains a vital contributor to the country's economy. It provides 12.8 million jobs, one-third the private-sector job opportunities, and employs a larger number of workers than the average American. Its share of national output has decreased since the Great Recession and its employment share has fallen below 12 percent. The manufacturing industry has been dealing with structural problems such as productivity, trade deficits and lower output. These issues are being slowly addressed but it remains to be seen what long-term implications they will have. The US manufacturing sector is in a position to rebound, but the United States needs to decide whether to make a resurgence happen.
Manufacturing is a capital intensive industry. The sector is changing as new technologies become available. Companies are investing in new technologies to increase productivity and the skills of workers. They also create a pipeline for future workers. Manufacturers invest in upskilling their workforce. These investments will help to increase their market share. In order to avoid future disruptions, the firms also work to strengthen their supply networks.
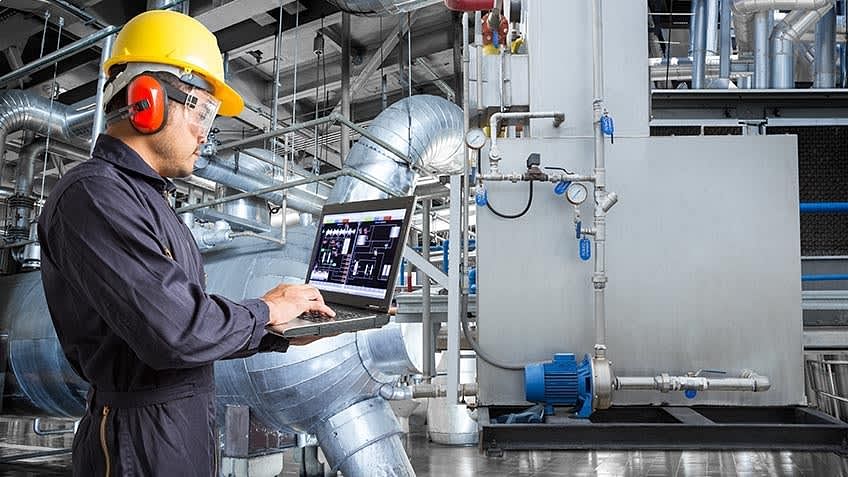
The supply chain challenges facing manufacturers are increasing in cost. These challenges can be addressed by the US by strengthening its innovation system. The US will need not engage in tariff wars with any country that wants to export to the US. However, it will be able to maintain open trade relations to keep its manufacturers competitive.
The United States has had a strong global presence for the past century. Because of this, the United States holds a large percentage of the global oil-and-gas demand. It is still the world's most important manufacturing country, but it is at risk. Its aging population and low international immigration are two reasons for this. It can also be more competitive by investing more in new technologies to improve its production efficiency and make it more durable.
US manufacturing sectors account for $2.3 Trillion in GDP. This figure represents 20 percent of the nation's capital investment and 35 percent of productivity growth. Manufacturing output reached a record high of $2.00 trillion in Q1 2018. This record-breaking figure for US manufacturing was set in Q1 2018. It's also the highest since the Great Recession. Furthermore, the manufacturing sector is performing better than the recovery of its labor market.
The United States has a global manufacturing presence that is second only to China. The nation's 60 percent exports are made up of manufacturing, which accounts for a significant portion of R&D spending. However, manufacturing output fell from the fourth to the first quarters of 2007 to 2009. Only a handful of states saw an increase in manufacturing output. Manufacturing has a stronger presence in the Eighth District States, and manufacturing output share has increased in many of those states.
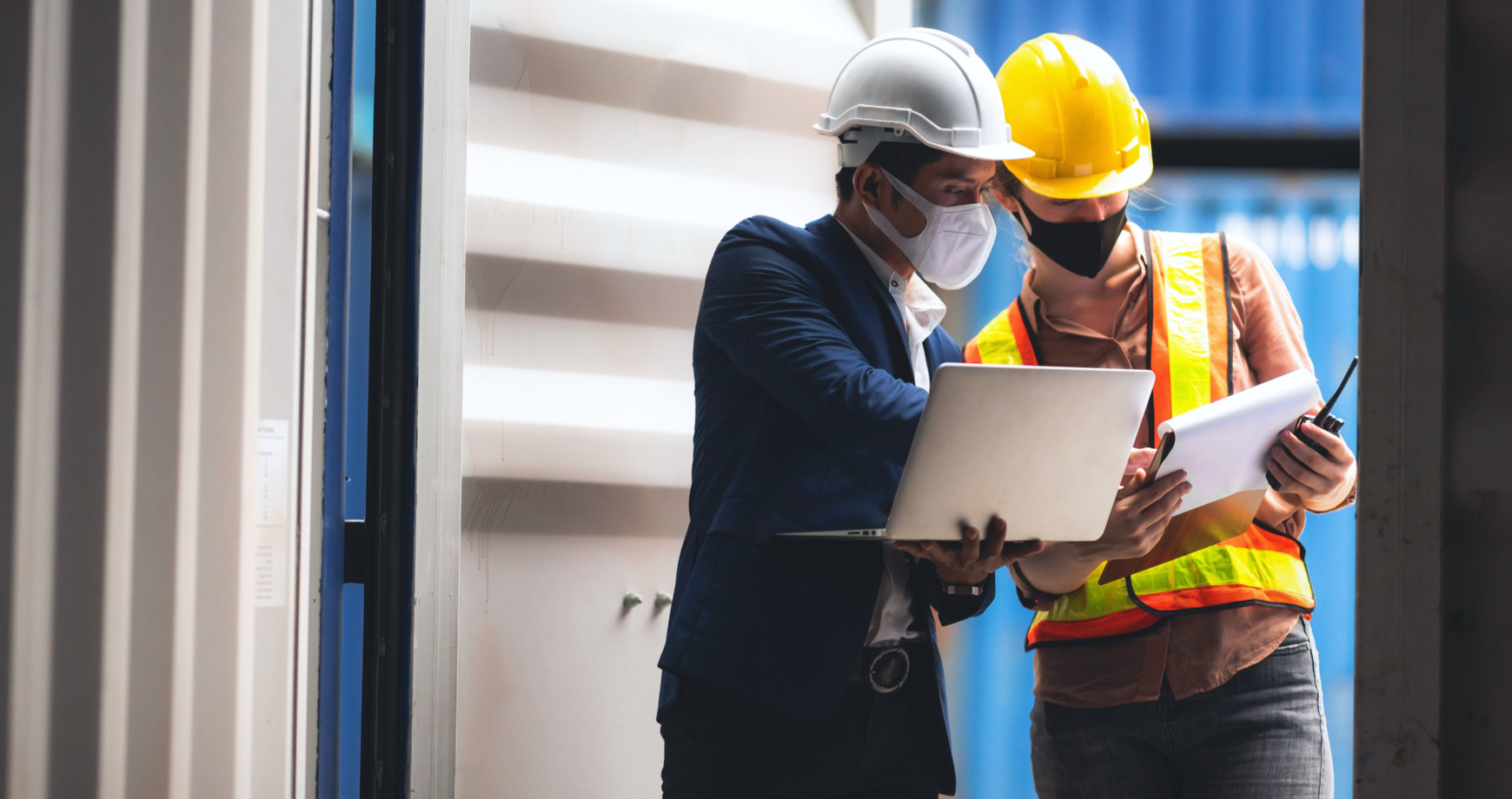
Manufacturing output was 15.2 percent below pre-pandemic levels in the fourth quarter of 2007. In the first quarter, 2009 saw a drop in manufacturing output of 6.4 percent. However, manufacturing output increased in Illinois and Indiana as well as Ohio and Michigan.
FAQ
What does it mean to warehouse?
A warehouse is a place where goods are stored until they are sold. It can be either an indoor or outdoor space. It could be one or both.
What are manufacturing and logistics?
Manufacturing refers the process of producing goods from raw materials through machines and processes. Logistics encompasses the management of all aspects associated with supply chain activities such as procurement, production planning, distribution and inventory control. It also includes customer service. Logistics and manufacturing are often referred to as one thing. It encompasses both the creation of products and their delivery to customers.
Why should you automate your warehouse?
Automation has become increasingly important in modern warehousing. Increased demand for efficient and faster delivery has resulted in a rise in e-commerce.
Warehouses must be able to quickly adapt to changing demands. To do so, they must invest heavily in technology. Automating warehouses has many benefits. Here are some reasons why it's worth investing in automation:
-
Increases throughput/productivity
-
Reduces errors
-
Accuracy is improved
-
Safety is boosted
-
Eliminates bottlenecks
-
Allows companies scale more easily
-
Increases efficiency of workers
-
The warehouse can be viewed from all angles.
-
Enhances customer experience
-
Improves employee satisfaction
-
It reduces downtime, and increases uptime
-
This ensures that quality products are delivered promptly
-
Removes human error
-
It ensures compliance with regulations
What do we need to know about Manufacturing Processes in order to learn more about Logistics?
No. You don't have to know about manufacturing processes before learning about logistics. Understanding the manufacturing process will allow you to better understand logistics.
Statistics
- According to a Statista study, U.S. businesses spent $1.63 trillion on logistics in 2019, moving goods from origin to end user through various supply chain network segments. (netsuite.com)
- Many factories witnessed a 30% increase in output due to the shift to electric motors. (en.wikipedia.org)
- In the United States, for example, manufacturing makes up 15% of the economic output. (twi-global.com)
- You can multiply the result by 100 to get the total percent of monthly overhead. (investopedia.com)
- Job #1 is delivering the ordered product according to specifications: color, size, brand, and quantity. (netsuite.com)
External Links
How To
How to Use Six Sigma in Manufacturing
Six Sigma is "the application statistical process control (SPC), techniques for continuous improvement." Motorola's Quality Improvement Department developed it at their Tokyo plant in Japan in 1986. Six Sigma is a method to improve quality through standardization and elimination of defects. Many companies have adopted Six Sigma in recent years because they believe that there are no perfect products and services. The main goal of Six Sigma is to reduce variation from the mean value of production. This means that if you take a sample of your product, then measure its performance against the average, you can find out what percentage of the time the process deviates from the norm. If this deviation is too big, you know something needs fixing.
Understanding the dynamics of variability within your business is the first step in Six Sigma. Once you've understood that, you'll want to identify sources of variation. You'll also want to determine whether these variations are random or systematic. Random variations occur when people do mistakes. Symmetrical variations are caused due to factors beyond the process. You could consider random variations if some widgets fall off the assembly lines. You might notice that your widgets always fall apart at the same place every time you put them together.
Once you have identified the problem, you can design solutions. You might need to change the way you work or completely redesign the process. You should then test the changes again after they have been implemented. If they don't work you need to rework them and come up a better plan.