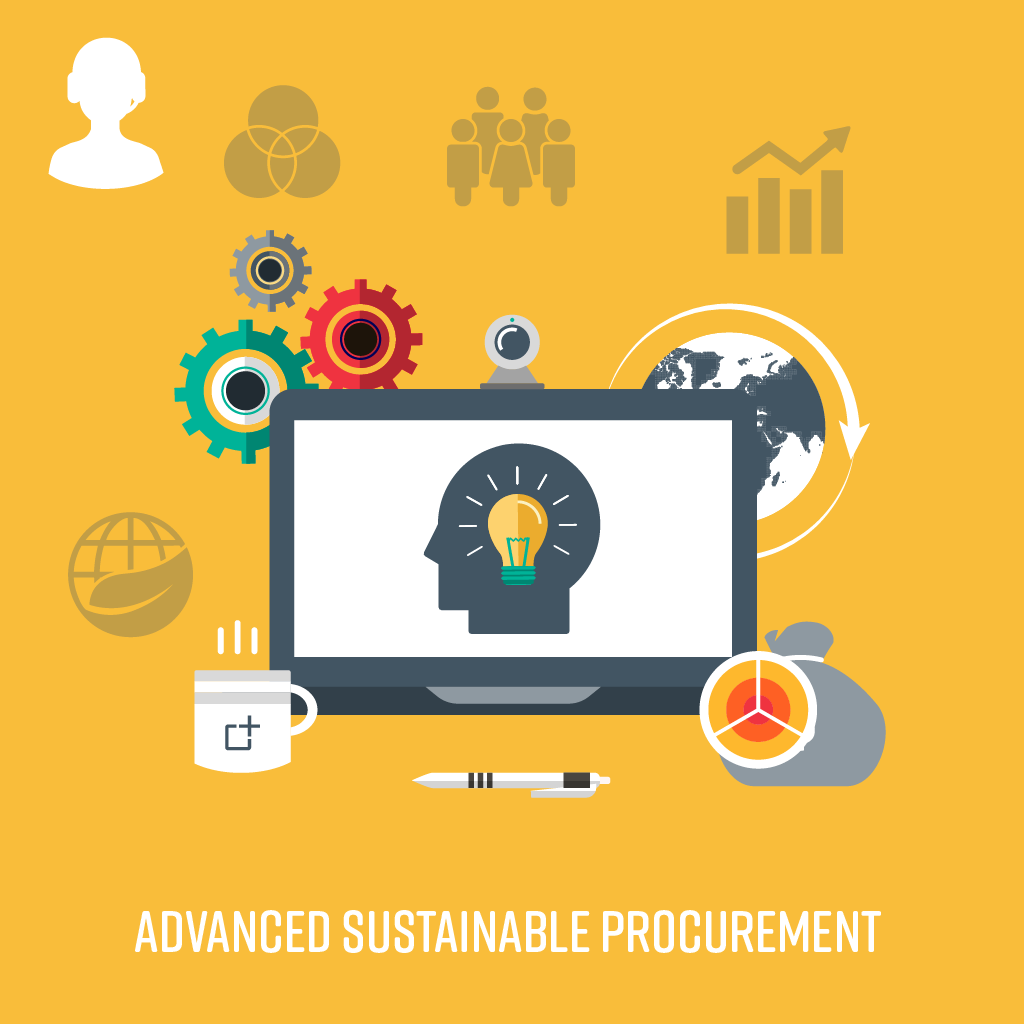
It is essential to have a well-organized media supply chain. Companies must invest in modern technology to ensure their content gets delivered to consumers in a timely manner. Using a cloud-based, purpose-built platform is a great way to ensure that your media assets are being used in the most effective way possible. It facilitates processes that can give you greater insight into your business.
Understanding the components of your media supply chain workflow is key to getting the best out of it. For example, the workflow may include quality control to ensure that your media files are in the right format, audio mapping, and codec. This is essential to ensure the content is delivered correctly and preserved. Having a good metadata framework also helps you understand what content is being delivered, which can help you find content faster.
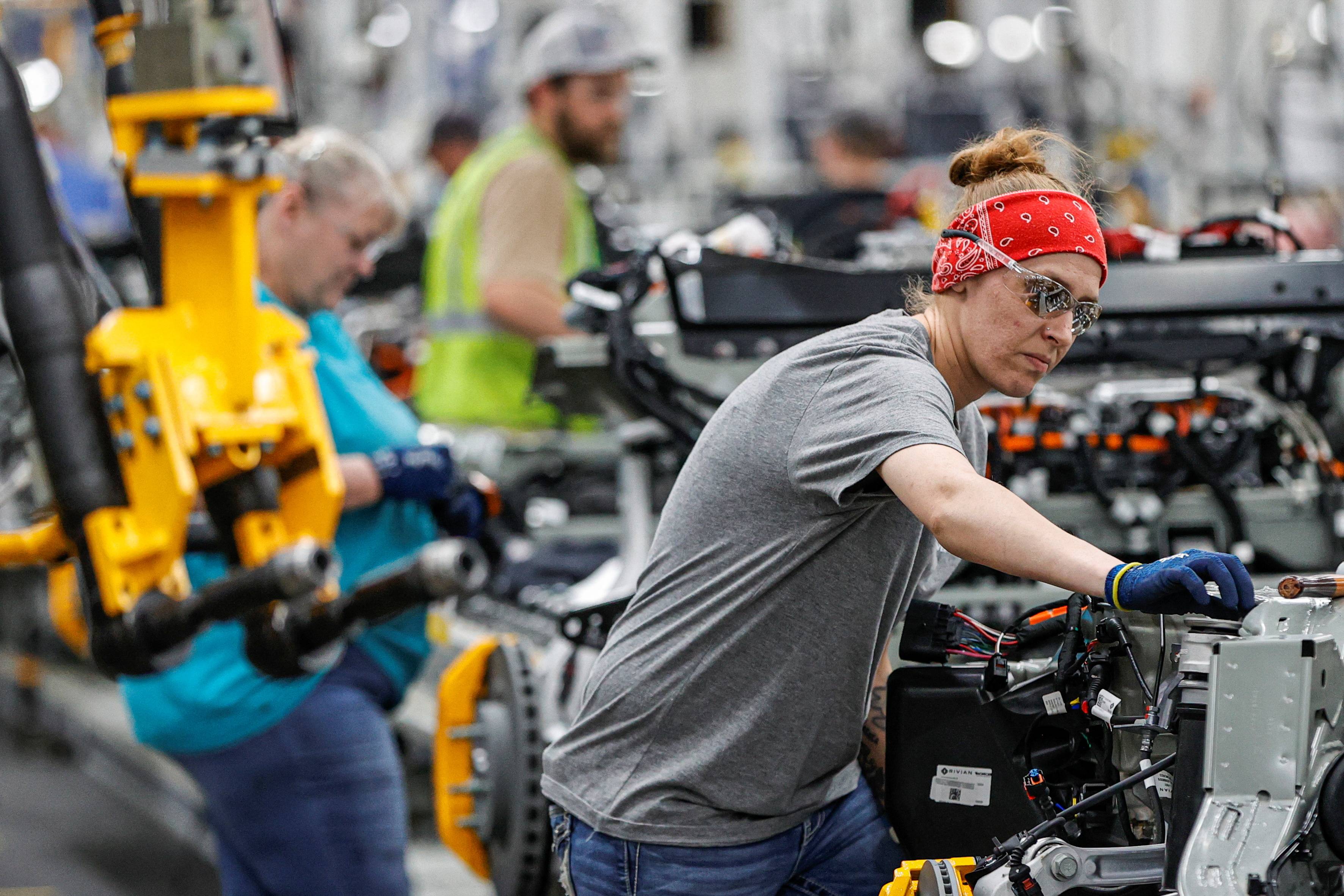
You may be able to receive content from third parties or other companies as part of your media supply chain workflow. This can pose challenges, as the files may arrive in various formats. The files may need to be processed before they can use. This might include changing the format, or transcoding master files into smaller proxy file. This could be expensive and impact your business continuity.
The media supply chain workflows are more complex than ever. Gone are the days of inserting tape onto a machine. Video editing technology and streaming services have revolutionized the way content is created. These technologies allow you to create multiple versions of the same piece of content. This ensures that you have the best quality. This will allow you to reduce costs and provide the highest quality content.
You will need to be able to understand the process involved in order to make the most of your media supply chain workflow. Expertise in server and client operating systems, networking, as well as media terminology is essential. Experience with cloud deployments is also required. If you're not sure how to do this, you may want to consult with an IT Analyst who has expertise in these areas.
The video engineer works closely alongside the client's team to establish a media supply channel workflow. They are responsible for improving functionality and working with vendors to deliver media to the end-user. They are also responsible to develop requirements for new features.
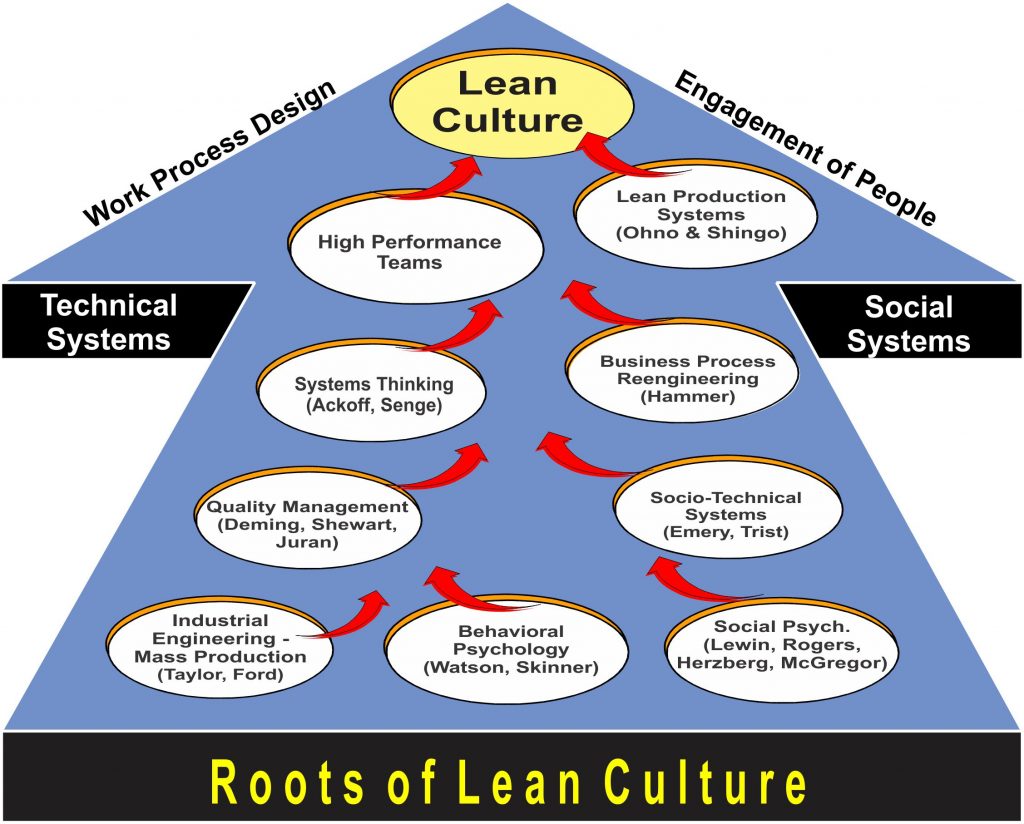
Paramount Global Media Supply Chain Platforms Operations workflows lead by the Director Product. They will collaborate with both internal and external collaborators in order to create and implement solutions that Paramount customers. They will provide regular feedback and review product requirements. They will also manage product development cycles that use Agile methodology. They will also communicate product requirements to development teams and oversee the translation of these requirements into the product.
FAQ
What are manufacturing & logistics?
Manufacturing refers the process of producing goods from raw materials through machines and processes. Logistics includes all aspects related to supply chain management, such as procurement, distribution planning, inventory control and transportation. As a broad term, manufacturing and logistics often refer to both the creation and delivery of products.
Why should you automate your warehouse?
Modern warehousing has seen automation take center stage. With the rise of ecommerce, there is a greater demand for faster delivery times as well as more efficient processes.
Warehouses have to be flexible to meet changing requirements. To do so, they must invest heavily in technology. The benefits of automating warehouses are numerous. Here are some of the reasons automation is worth your investment:
-
Increases throughput/productivity
-
Reduces errors
-
Improves accuracy
-
Safety enhancements
-
Eliminates bottlenecks
-
Companies can scale up more easily
-
This makes workers more productive
-
It gives visibility to everything that happens inside the warehouse
-
Enhances customer experience
-
Improves employee satisfaction
-
Reducing downtime and increasing uptime
-
Quality products delivered on time
-
Removes human error
-
This helps to ensure compliance with regulations
How can manufacturing reduce production bottlenecks?
The key to avoiding bottlenecks in production is to keep all processes running smoothly throughout the entire production cycle, from the time you receive an order until the time when the product ships.
This includes both planning for capacity and quality control.
Continuous improvement techniques like Six Sigma are the best way to achieve this.
Six Sigma is a management system used to improve quality and reduce waste in every aspect of your organization.
It focuses on eliminating variation and creating consistency in your work.
Statistics
- It's estimated that 10.8% of the U.S. GDP in 2020 was contributed to manufacturing. (investopedia.com)
- According to a Statista study, U.S. businesses spent $1.63 trillion on logistics in 2019, moving goods from origin to end user through various supply chain network segments. (netsuite.com)
- Many factories witnessed a 30% increase in output due to the shift to electric motors. (en.wikipedia.org)
- [54][55] These are the top 50 countries by the total value of manufacturing output in US dollars for its noted year according to World Bank.[56] (en.wikipedia.org)
- In 2021, an estimated 12.1 million Americans work in the manufacturing sector.6 (investopedia.com)
External Links
How To
How to use 5S to increase Productivity in Manufacturing
5S stands to stand for "Sort", “Set In Order", “Standardize", and "Store". Toyota Motor Corporation was the first to develop the 5S approach in 1954. This methodology helps companies improve their work environment to increase efficiency.
This method aims to standardize production processes so that they are repeatable, measurable and predictable. It means tasks like cleaning, sorting or packing, labeling, and storing are done every day. Through these actions, workers can perform their jobs more efficiently because they know what to expect from them.
Implementing 5S requires five steps. These are Sort, Set In Order, Standardize. Separate. And Store. Each step requires a different action, which increases efficiency. If you sort items, it makes them easier to find later. When you arrange items, you place them together. After you have divided your inventory into groups you can store them in easy-to-reach containers. Labeling your containers will ensure that everything is correctly labeled.
Employees need to reflect on how they do their jobs. Employees need to be able understand their motivations and discover alternative ways to do them. In order to use the 5S system effectively, they must be able to learn new skills.
The 5S method increases efficiency and morale among employees. They feel more motivated to work towards achieving greater efficiency as they see the results.