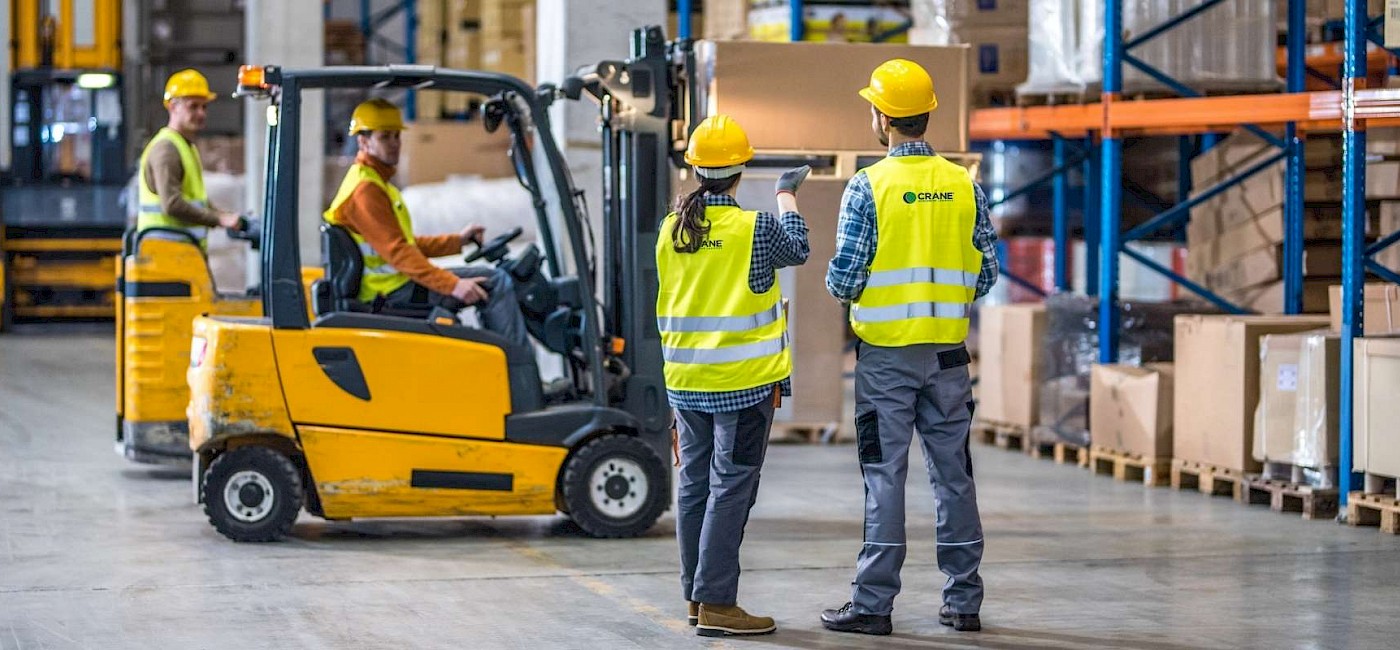
Purchasing Managers, also called Materials Managers, are responsible in sourcing and coordinating all purchases. They interact with suppliers, vendors, and other purchasing agents. They need to have a good understanding of the company's purchasing process, and how to improve it. They must also know how to negotiate the best deal for the company.
A purchasing manager also needs to have accurate and current records regarding purchases. They analyse customer requirements, assess financial reports, evaluate vendor capabilities and evaluate price trends. They also coordinate purchasing activities. They may be required to work overtime if the company needs supplies from international markets.
As well as managing inventory and logistics, purchasing managers coordinate and manage them. They determine the best method of purchasing and ensure that purchased items are in compliance with company quality standards. They help to manage budgets and coordinate with their staff to ensure that purchases can be made at the most affordable price. They are also able to negotiate contracts and find the best suppliers.
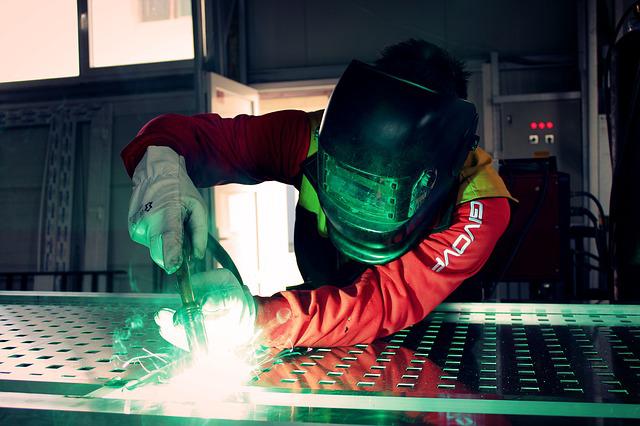
The time schedules of all purchasing staff are also monitored and managed by the Purchasing Managers. They also assess the quality of purchased goods and the delivery time. They meet with suppliers and buyers and visit their distribution facilities. They also check that suppliers are adhering to the terms of the contract. They may also have responsibility for team building and disciplinary issues.
A Purchasing Manager should have exceptional communication skills, analytic abilities, and strategic thinking skills. They should be able analyze the impact of different products on the company. They must be able manage suppliers and their relationships. They should also be able take business decisions and increase sales. They must be able deal with complicated purchases. They must be able to evaluate new vendors, analyze their capabilities, and select the best vendor for the company.
A bachelor's degree or equivalent in business is required of most purchasing managers. Experience in supply chain and inventory management is also an asset. They should also be familiar with Microsoft Office and other software programs.
The best purchasing managers should be able find the best deals and negotiate favorable contracts. They must also be able coordinate all purchasing activities, manage inventories and track supplier and vendor performance. They should also possess the ability to manage a small team of purchasing agents.
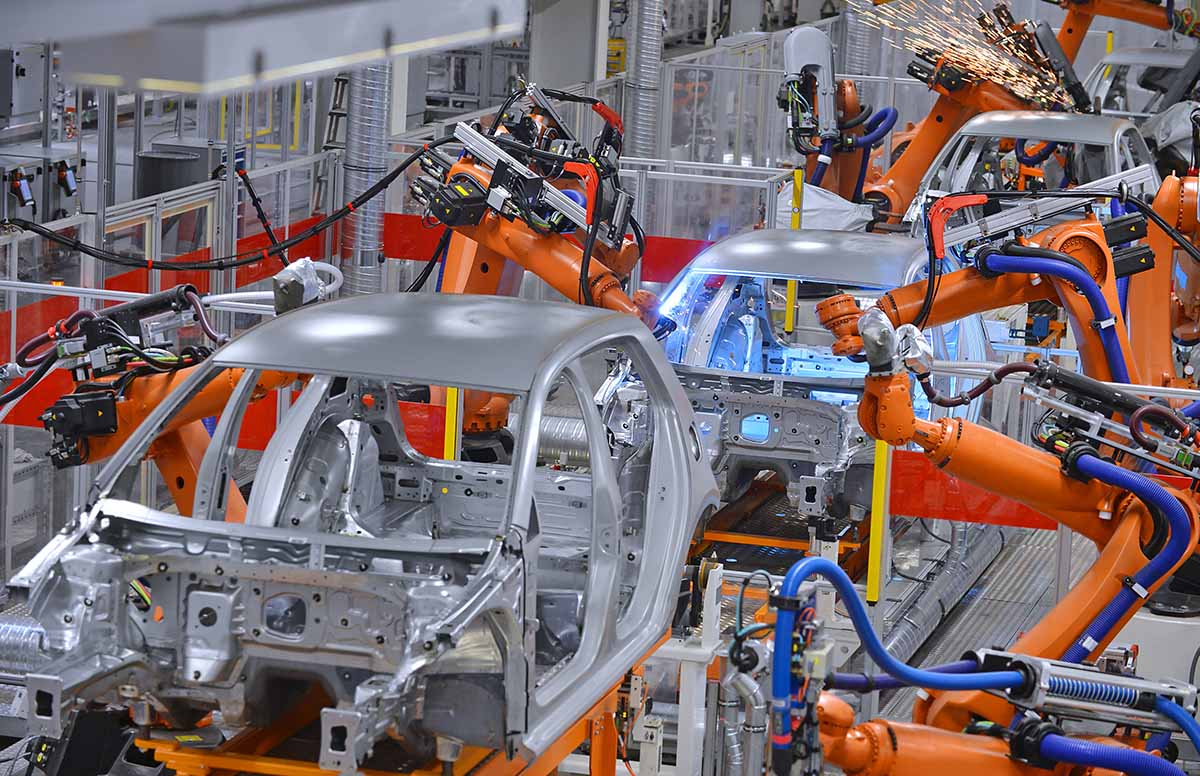
It is important that the job description for a purchase manager mentions how essential purchasing is to the company's success. It should also mention how important it is for the company to stay ahead of the curve. It should also mention how the company values its employees' work-life balance. It should include a call for action to encourage applicants.
If the company must purchase material or equipment for an overseas market, Purchasing managers might also be required to work overtime. They might also need to meet with sellers and vendors or attend trade shows.
FAQ
Is it necessary to be familiar with Manufacturing Processes before we learn about Logistics.
No. No. Understanding the manufacturing process will allow you to better understand logistics.
Are there ways to automate parts of manufacturing?
Yes! Yes! Automation has existed since ancient times. The Egyptians invent the wheel thousands of year ago. We now use robots to help us with assembly lines.
In fact, there are several applications of robotics in manufacturing today. These include:
-
Line robots
-
Robot welding
-
Robot painting
-
Robotics inspection
-
Robots that produce products
Automation can be applied to manufacturing in many other ways. 3D printing makes it possible to produce custom products in a matter of days or weeks.
Why is logistics so important in manufacturing?
Logistics are an integral part any business. Logistics can help you achieve amazing results by helping to manage product flow from raw materials to finished products.
Logistics play an important role in reducing costs as well as increasing efficiency.
Statistics
- You can multiply the result by 100 to get the total percent of monthly overhead. (investopedia.com)
- It's estimated that 10.8% of the U.S. GDP in 2020 was contributed to manufacturing. (investopedia.com)
- [54][55] These are the top 50 countries by the total value of manufacturing output in US dollars for its noted year according to World Bank.[56] (en.wikipedia.org)
- According to the United Nations Industrial Development Organization (UNIDO), China is the top manufacturer worldwide by 2019 output, producing 28.7% of the total global manufacturing output, followed by the United States, Japan, Germany, and India.[52][53] (en.wikipedia.org)
- According to a Statista study, U.S. businesses spent $1.63 trillion on logistics in 2019, moving goods from origin to end user through various supply chain network segments. (netsuite.com)
External Links
How To
How to Use Just-In-Time Production
Just-intime (JIT), a method used to lower costs and improve efficiency in business processes, is called just-in-time. It's the process of obtaining the right amount and timing of resources when you need them. This means that your only pay for the resources you actually use. The term was first coined by Frederick Taylor, who developed his theory while working as a foreman in the early 1900s. After observing how workers were paid overtime for late work, he realized that overtime was a common practice. He then concluded that if he could ensure that workers had enough time to do their job before starting to work, this would improve productivity.
JIT teaches you to plan ahead and prepare everything so you don’t waste time. The entire project should be looked at from start to finish. You need to ensure you have enough resources to tackle any issues that might arise. You will have the resources and people to solve any problems you anticipate. This will prevent you from spending extra money on unnecessary things.
There are many JIT methods.
-
Demand-driven JIT: You order the parts and materials you need for your project every other day. This will let you track the amount of material left over after you've used it. This will allow you to calculate how long it will take to make more.
-
Inventory-based : You can stock the materials you need in advance. This allows you to forecast how much you will sell.
-
Project-driven: This method allows you to set aside enough funds for your project. Once you have an idea of how much material you will need, you can purchase the necessary materials.
-
Resource-based JIT: This is the most popular form of JIT. You assign certain resources based off demand. You might assign more people to help with orders if there are many. If you don’t have many orders you will assign less people to the work.
-
Cost-based : This is similar in concept to resource-based. But here, you aren't concerned about how many people your company has but how much each individual costs.
-
Price-based: This is similar to cost-based but instead of looking at individual workers' salaries, you look at the total company price.
-
Material-based: This is quite similar to cost-based, but instead of looking at the total cost of the company, you're concerned with how much raw materials you spend on average.
-
Time-based JIT: A variation on resource-based JIT. Instead of worrying about how much each worker costs, you can focus on how long the project takes.
-
Quality-based JIT is another variant of resource-based JIT. Instead of thinking about the cost of each employee or the time it takes to produce something, you focus on how good your product quality.
-
Value-based JIT: This is the latest form of JIT. This is where you don't care about how the products perform or whether they meet customers' expectations. Instead, you're focused on how much value you add to the market.
-
Stock-based is an inventory-based system that measures the number of items produced at any given moment. This method is useful when you want to increase production while decreasing inventory.
-
Just-in-time planning (JIT): This is a combination JIT and supply-chain management. It is the process that schedules the delivery of components within a short time of their order. It is essential because it reduces lead-times and increases throughput.