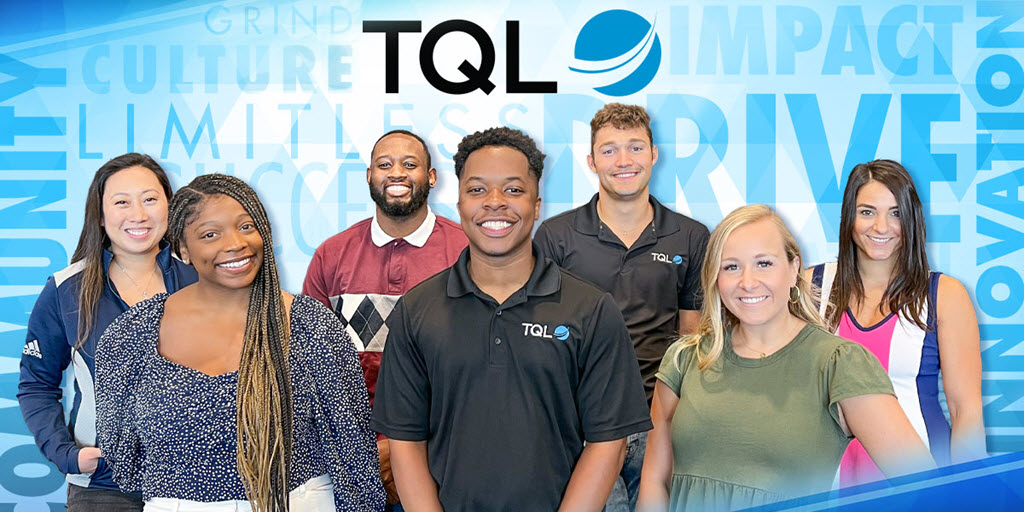
Los Angeles logistics jobs range from small courier projects to large warehouse projects. No matter the job, you'll be working with a professional team to ensure that your shipments make it to their destination on time and safely.
Find the best supply chain and logistics companies in your area with GoodFirms.
We will narrow down the list by using our extensive database, and in-depth research. Even worse, our team will let you know which companies to avoid.
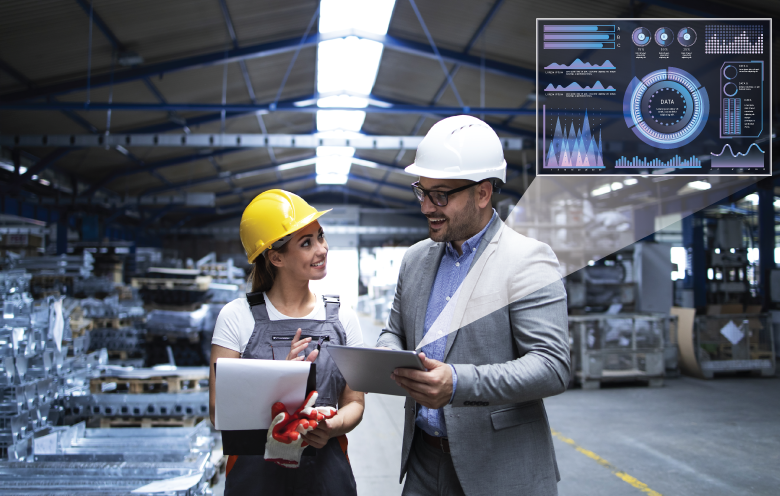
Los Angeles's Optimum Recruitment Supply Chain is your go-to source for all things logistics and supply chains. We can connect you to the perfect candidate, whether it's a VP for Logistics or a senior sales representative.
Top-rated Los Angeles Logistics Company
As a leading third-party logistics (or 3PL) provider, we design and operate global supply chain and logistics solutions. Our services include global freight forwarding and customs management, as well as shipment consolidation and deconsolidation.
Logistics & Shipping Specialist Jobs in Los Angeles, CA
We have a large number of jobs for warehouse workers, logisticians and managers. The latest job openings are listed on our free job board. We're happy to work with the leading employers in the United States and are dedicated finding you the best job.
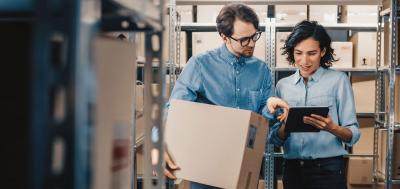
Los Angeles, CA Logistics Manager
Los Angeles has an average annual salary of $57K for a logistics director. You can find 1,240 jobs for logistics managers in Los Angeles, but to be noticed you need a special set of skills. The most impressive logistics managers are those with an eye for detail and a strong commitment to the success of their team. Your qualifications should include a track record of success, leadership skills, and customer service.
FAQ
How is a production manager different from a producer planner?
A production planner is more involved in the planning phase of the project than a project manger.
What does manufacturing mean?
Manufacturing Industries are businesses that produce products for sale. These products are sold to consumers. These companies use a variety processes such as distribution, retailing and management to accomplish their purpose. They create goods from raw materials, using machines and various other equipment. This includes all types and varieties of manufactured goods, such as food items, clothings, building supplies, furnitures, toys, electronics tools, machinery vehicles, pharmaceuticals medical devices, chemicals, among others.
What does it mean to warehouse?
A warehouse is a place where goods are stored until they are sold. It can be either an indoor or outdoor space. It could be one or both.
What jobs are available in logistics?
There are many types of jobs in logistics. These are some of the jobs available in logistics:
-
Warehouse workers – They load, unload and transport pallets and trucks.
-
Transportation drivers: They drive trucks and trailers and deliver goods and make pick-ups.
-
Freight handlers: They sort and package freight in warehouses.
-
Inventory managers - They oversee the inventory of goods in warehouses.
-
Sales reps are people who sell products to customers.
-
Logistics coordinators are responsible for organizing and planning logistics operations.
-
Purchasing agents: They are responsible for purchasing goods and services to support company operations.
-
Customer service representatives - Answer calls and email from customers.
-
Shipping clerks - They process shipping orders and issue bills.
-
Order fillers - They fill orders based on what is ordered and shipped.
-
Quality control inspectors – They inspect incoming and outgoing products to ensure that there are no defects.
-
Others - There are many types of jobs in logistics such as transport supervisors and cargo specialists.
What do we need to know about Manufacturing Processes in order to learn more about Logistics?
No. You don't have to know about manufacturing processes before learning about logistics. Knowing about manufacturing processes will help you understand how logistics works.
Statistics
- According to a Statista study, U.S. businesses spent $1.63 trillion on logistics in 2019, moving goods from origin to end user through various supply chain network segments. (netsuite.com)
- Many factories witnessed a 30% increase in output due to the shift to electric motors. (en.wikipedia.org)
- According to the United Nations Industrial Development Organization (UNIDO), China is the top manufacturer worldwide by 2019 output, producing 28.7% of the total global manufacturing output, followed by the United States, Japan, Germany, and India.[52][53] (en.wikipedia.org)
- In the United States, for example, manufacturing makes up 15% of the economic output. (twi-global.com)
- In 2021, an estimated 12.1 million Americans work in the manufacturing sector.6 (investopedia.com)
External Links
How To
How to Use Six Sigma in Manufacturing
Six Sigma is "the application statistical process control (SPC), techniques for continuous improvement." Motorola's Quality Improvement Department developed it at their Tokyo plant in Japan in 1986. Six Sigma's basic concept is to improve quality and eliminate defects through standardization. This method has been adopted by many companies in recent years as they believe there are no perfect products or services. Six Sigma's primary goal is to reduce variation from the average value of production. This means that if you take a sample of your product, then measure its performance against the average, you can find out what percentage of the time the process deviates from the norm. If the deviation is excessive, it's likely that something needs to be fixed.
Understanding how your business' variability is a key step towards Six Sigma implementation is the first. Once you have a good understanding of the basics, you can identify potential sources of variation. Also, you will need to identify the sources of variation. Random variations are caused when people make mistakes. While systematic variations are caused outside of the process, they can occur. These are, for instance, random variations that occur when widgets are made and some fall off the production line. However, if you notice that every time you assemble a widget, it always falls apart at exactly the same place, then that would be a systematic problem.
Once you've identified the problem areas you need to find solutions. It might mean changing the way you do business or redesigning it entirely. After implementing the new changes, you should test them again to see if they worked. If they fail, you can go back to the drawing board to come up with a different plan.