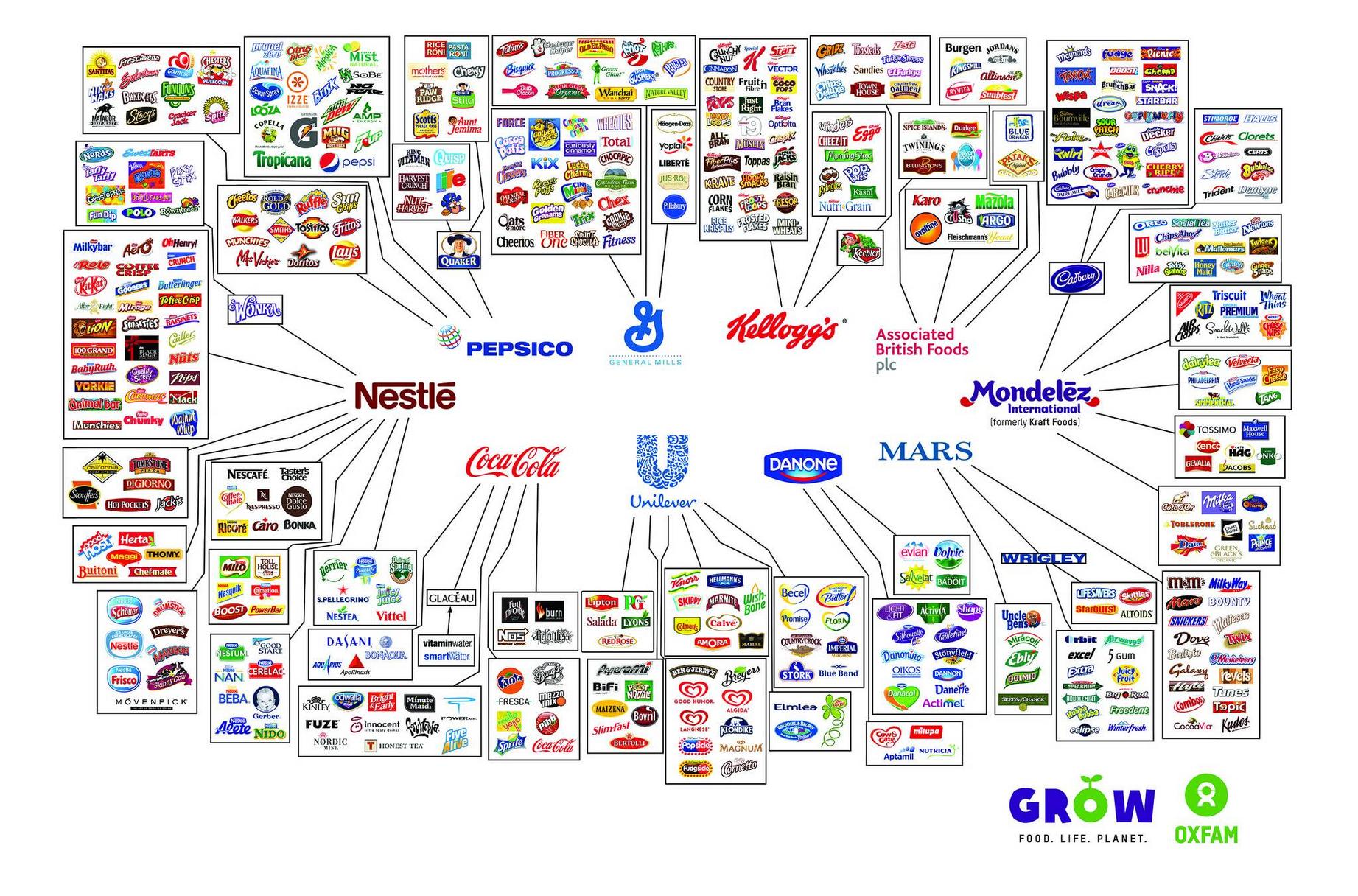
Denver is a city in Colorado that offers a wide variety of jobs. It also has several logistics companies which offer a variety of logistics services. Some of these include freight forwarding, trucking, and logistics & supply chain consulting.
If you are interested in working in the logistics industry, there are a few different jobs that you can consider, including dispatch manager, transportation director, and warehouse associate. All these positions are in charge of making sure the logistics within an organization run smoothly.
Dispatch Manager
A dispatch manager is responsible for coordinating and directing the activities of a team that works in a warehouse or a call center. This includes evaluating productivity, training new employees, delegating work, and coordinating workloads of team members. Dispatch managers usually have a bachelor's degree in business management or logistics and experience with workflow organization.
Transportation Director
Transportation directors are responsible for the logistics of a school, governmental department or company. It involves establishing distribution routes and arranging transportation methods, such as buses or trucks to transport goods from one place to another.
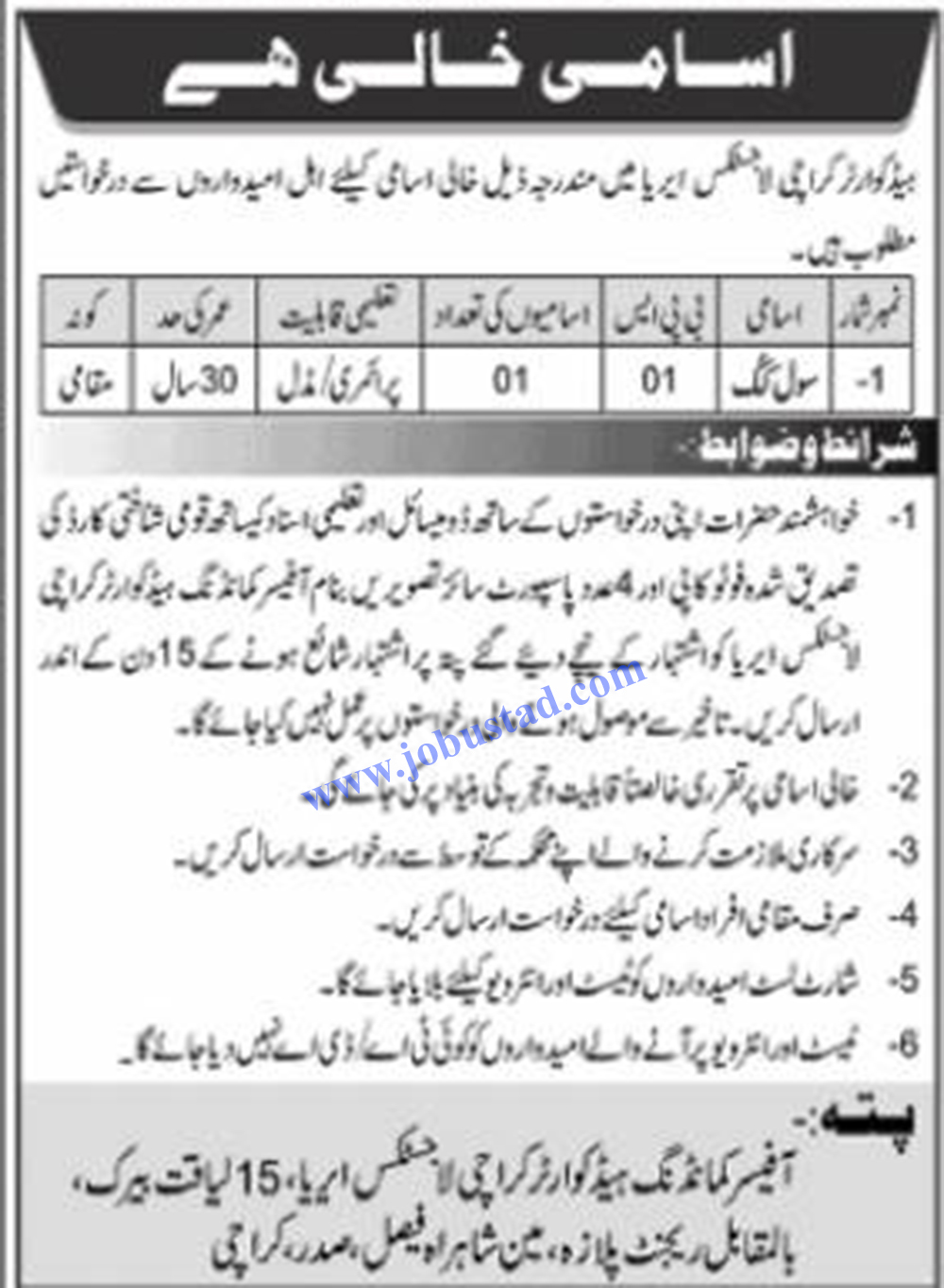
This career is for people who are looking to work at a government or larger company. As this is a highly-competitive job, you will need excellent organizational skills as well as the willingness to work long shifts.
Warehouse Associate
A warehouse associate may be the right job for you if your schedule is flexible and you don't want to compete with other candidates. A warehouse associate is typically responsible for handling smaller projects, such as picking shipments and packing products. They may also be in charge of moving merchandise from one location to another.
Create a Monster account to begin your search for a logistics job. This will let you be notified when there are new logistics jobs available near you.
You will also be able receive expert advice on how to maximize your job application and how to negotiate your wage, among other things.
Logistic Manager
If you want to become a logistics manager, you should have at least a bachelor's degree in supply chain management or business administration. It is necessary to have a minimum of a year's professional experience in warehouse environments, and strong organization skills. For a career as a senior logistics director, you may also need a master's in supply chain or a related field.
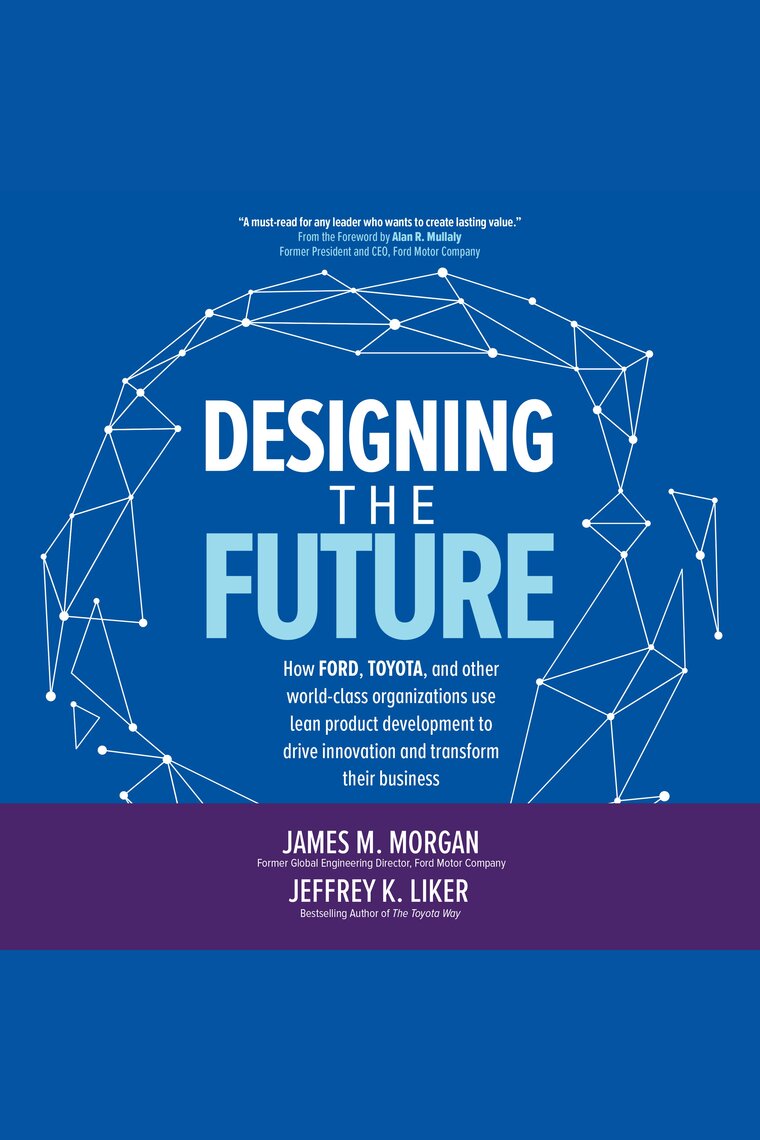
Logistik Analyst
A logistic analyst is responsible for monitoring the logistics of an organization and making changes to help it better achieve its goals. This involves evaluating inventory levels and scheduling delivery times. A logistics analyst must hold a bachelor's in business or engineering, and have prior experience in the logistics of an industry.
There are many job opportunities in the logistics industry. Set up your free Monster account today if you're ready to begin a career. You'll have the best chances to find the logistics jobs that are right for you if you create a free account on Monster.
FAQ
How can we improve manufacturing efficiency?
First, identify the factors that affect production time. Then we need to find ways to improve these factors. You can start by identifying the most important factors that impact production time. Once you have identified the factors, then try to find solutions.
Are there ways to automate parts of manufacturing?
Yes! Yes. The Egyptians created the wheel thousands years ago. Today, robots assist in the assembly of lines.
There are many applications for robotics in manufacturing today. These include:
-
Line robots
-
Robot welding
-
Robot painting
-
Robotics inspection
-
Robots that make products
Automation could also be used to improve manufacturing. 3D printing is a way to make custom products quickly and without waiting weeks or months for them to be manufactured.
Is it necessary to be familiar with Manufacturing Processes before we learn about Logistics.
No. No. Knowing about manufacturing processes will help you understand how logistics works.
Why automate your warehouse
Modern warehouses are increasingly dependent on automation. E-commerce has increased the demand for quicker delivery times and more efficient processes.
Warehouses should be able adapt quickly to new needs. They must invest heavily in technology to do this. Automation of warehouses offers many benefits. Here are some of the reasons automation is worth your investment:
-
Increases throughput/productivity
-
Reduces errors
-
Increases accuracy
-
Safety Boosts
-
Eliminates bottlenecks
-
Companies can scale up more easily
-
Increases efficiency of workers
-
The warehouse can be viewed from all angles.
-
Enhances customer experience
-
Improves employee satisfaction
-
Reducing downtime and increasing uptime
-
Quality products delivered on time
-
Eliminates human error
-
This helps to ensure compliance with regulations
How does a Production Planner differ from a Project Manager?
A production planner is more involved in the planning phase of the project than a project manger.
Statistics
- According to a Statista study, U.S. businesses spent $1.63 trillion on logistics in 2019, moving goods from origin to end user through various supply chain network segments. (netsuite.com)
- According to the United Nations Industrial Development Organization (UNIDO), China is the top manufacturer worldwide by 2019 output, producing 28.7% of the total global manufacturing output, followed by the United States, Japan, Germany, and India.[52][53] (en.wikipedia.org)
- You can multiply the result by 100 to get the total percent of monthly overhead. (investopedia.com)
- Many factories witnessed a 30% increase in output due to the shift to electric motors. (en.wikipedia.org)
- In 2021, an estimated 12.1 million Americans work in the manufacturing sector.6 (investopedia.com)
External Links
How To
How to use 5S to increase Productivity in Manufacturing
5S stands for "Sort", 'Set In Order", 'Standardize', & Separate>. The 5S methodology was developed at Toyota Motor Corporation in 1954. This methodology helps companies improve their work environment to increase efficiency.
The idea behind standardizing production processes is to make them repeatable and measurable. Cleaning, sorting and packing are all done daily. This knowledge allows workers to be more efficient in their work because they are aware of what to expect.
There are five steps that you need to follow in order to implement 5S. Each step is a different action that leads to greater efficiency. For example, when you sort things, you make them easy to find later. When you set items in an order, you put items together. Then, after you separate your inventory into groups, you store those groups in containers that are easy to access. Make sure everything is correctly labeled when you label your containers.
Employees need to reflect on how they do their jobs. Employees need to be able understand their motivations and discover alternative ways to do them. To implement the 5S system, employees must acquire new skills and techniques.
The 5S method not only increases efficiency but also boosts morale and teamwork. Once they start to notice improvements, they are motivated to keep working towards their goal of increasing efficiency.