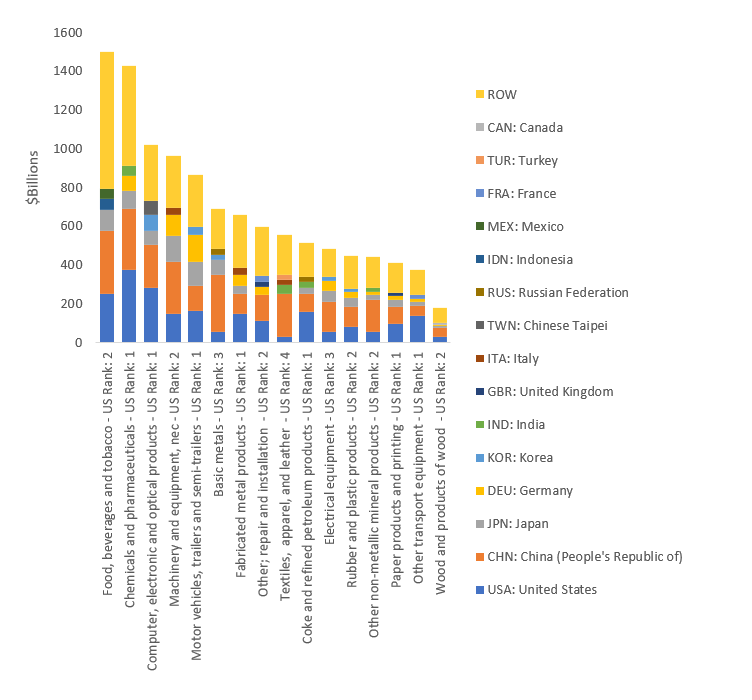
DMAIC (Define, Measure, Analyze. Improve. Control) is a model of process improvement that comprises five steps. Six Sigma experts use it frequently to make improvements to quality in a firm, but can also implement it independently as a structured process for continuous improvement.
Dmaic is an approach to quality that aims at reducing defects, cost and rework. It is a method that has been proven to improve customer satisfaction by ensuring products of high-quality, are efficient and perform consistently.
DMAIC can be an effective way to resolve issues within a company. It can also be used to improve processes that impact customer satisfaction, quality of products, cost reductions and cycle times. It is an important part of every quality improvement program.
The DMAIC is a structured method of problem solving that helps organizations eliminate the root causes behind a particular issue. The model uses a top-down approach and a systematic methodology that makes it easier for teams to implement foolproof and data-driven changes.
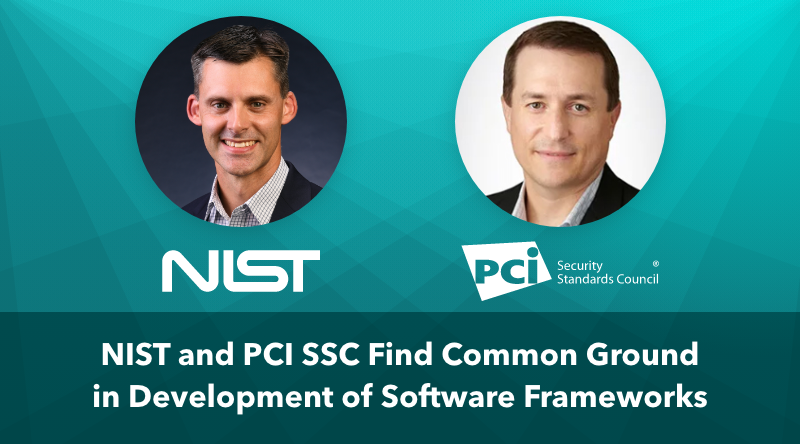
It is an important tool in Lean Six Sigma as it gives teams a clear and structured way to solve quality issues. This is important, especially for complex problems with unknown causes and the risk of inaction.
It is important that you understand the criteria before selecting a DMAIC. It's also important to be aware of the tools available during this process. These include fishbone charts and Pareto chart.
Once you've selected a project and qualified it for DMAIC, you can begin the process by identifying its needs and goals. It's best to select DMAIC-qualified projects that are pertinent to the state of business today.
DMAIC's Define phase involves defining clearly the problem and scope of the improvements. This is often done in a formal project charter, but it can be more informal as well. It identifies the CTQ (critical to quality) issues, the core business processes involved and the scope of the work.
This is an important step in the DMAIC process because it enables teams to understand which issues must be addressed first, how much work they will need to do and what metrics they should use to track success. This step also allows teams to identify a project champion, which is crucial for the success of a DMAIC project.
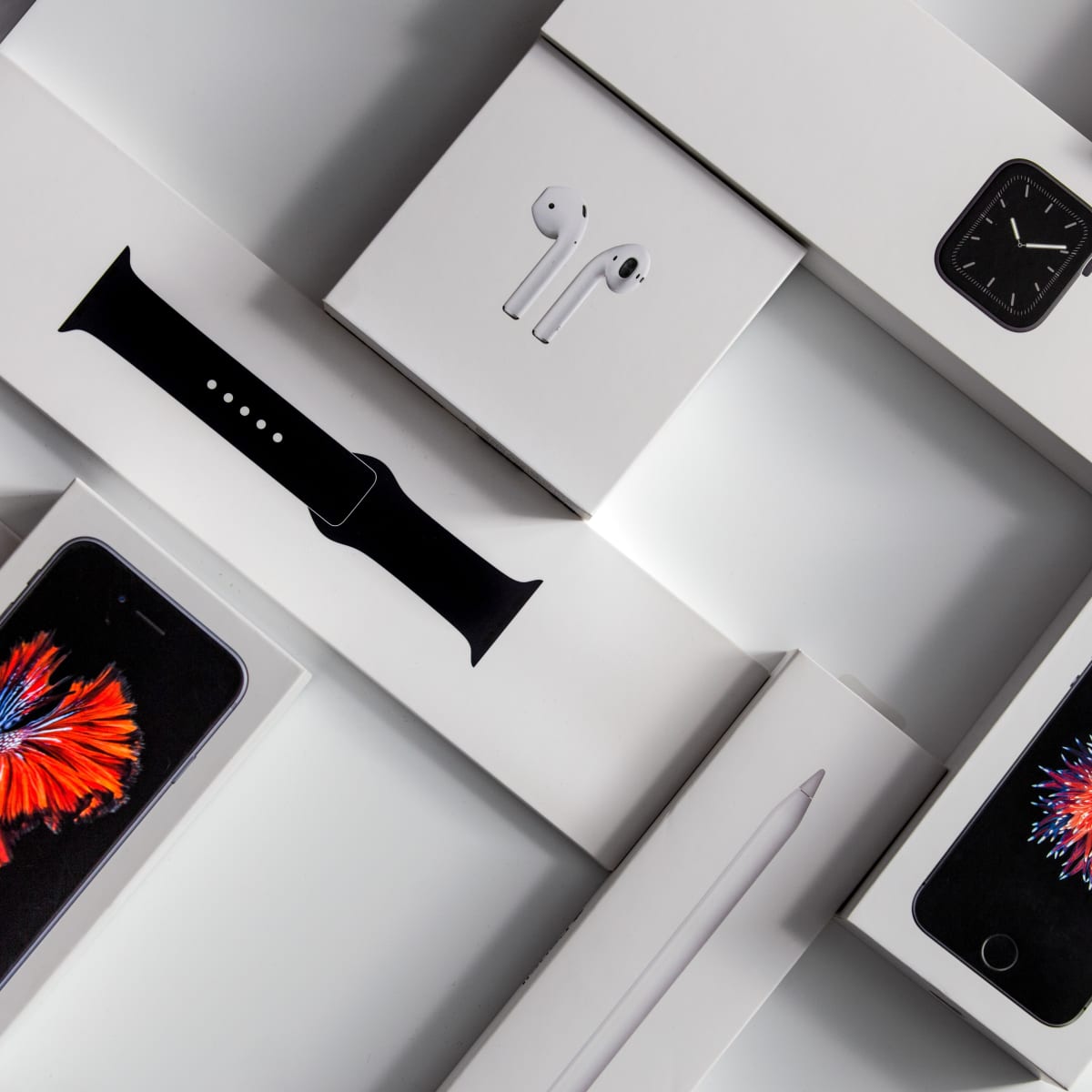
During the Measure phase, the teams collect and compare data to determine the state of the goal. They then use this information to determine gaps between the two states and identify opportunities for improvement. This can be done by implementing a variety of different tools, such as scatterplots, frequency plots or statistical analysis.
After analyzing the data, teams identify potential solutions to the problem and test them to make sure they are working. They implement the solutions, and confirm that they have measurable and durable results.
FAQ
What is production planning?
Production Planning refers to the development of a plan for every aspect of production. This document is designed to make sure everything is ready for when you're ready to shoot. It should also provide information about how best to produce the best results while on set. This includes information on shooting times, locations, cast lists and crew details.
The first step is to decide what you want. You might have an idea of where you want to film, or you may have specific locations or sets in mind. Once you've identified the locations and scenes you want to use, you can begin to plan what elements you need for each scene. Perhaps you have decided that you need to buy a car but aren't sure which model. This is where you can look up car models online and narrow down your options by choosing from different makes and models.
After you have chosen the right car, you will be able to begin thinking about accessories. What about additional seating? Or maybe you just need someone to push the car around. You may want to change the interior's color from black or white. These questions will help to determine the style and feel of your car. Also, think about what kind of shots you would like to capture. What type of shots will you choose? Maybe you want to show the engine and the steering wheel. These details will help identify the exact car you wish to film.
Once you've determined the above, it is time to start creating a calendar. You can use a schedule to determine when and where you need it to be shot. You will need to know when you have to be there, what time you have to leave and when your return home. It will help everyone know exactly what they have to do and when. If you need to hire extra staff, you can make sure you book them in advance. It is not worth hiring someone who won’t show up because you didn’t tell him.
You will need to factor in the days that you have to film when creating your schedule. Some projects only take one or two days, while others may last weeks. When creating your schedule, be aware of whether you need more shots per day. Multiple takes at the same place will result in higher costs and longer completion times. You can't be certain if you will need multiple takes so it is better not to shoot too many.
Budgeting is another crucial aspect of production plan. A realistic budget will help you work within your means. If you have to reduce your budget due to unexpected circumstances, you can always lower it later. However, it is important not to overestimate the amount that you will spend. If you underestimate the cost of something, you will have less money left after paying for other items.
Production planning is a detailed process. But, once you understand the workings of everything, it becomes easier for future projects to be planned.
What skills is required for a production planner?
Production planners must be flexible, organized, and able handle multiple tasks. You must also be able to communicate effectively with clients and colleagues.
Why should you automate your warehouse?
Modern warehouses are increasingly dependent on automation. E-commerce has increased the demand for quicker delivery times and more efficient processes.
Warehouses have to be flexible to meet changing requirements. To do so, they must invest heavily in technology. The benefits of automating warehouses are numerous. These are just a few reasons to invest in automation.
-
Increases throughput/productivity
-
Reduces errors
-
Improves accuracy
-
Safety Boosts
-
Eliminates bottlenecks
-
Allows companies to scale more easily
-
This makes workers more productive
-
It gives visibility to everything that happens inside the warehouse
-
Enhances customer experience
-
Improves employee satisfaction
-
It reduces downtime, and increases uptime
-
Quality products delivered on time
-
Removing human error
-
It ensures compliance with regulations
What do you mean by warehouse?
A warehouse is a place where goods are stored until they are sold. It can be indoors or out. It may also be an indoor space or an outdoor area.
Statistics
- In the United States, for example, manufacturing makes up 15% of the economic output. (twi-global.com)
- Job #1 is delivering the ordered product according to specifications: color, size, brand, and quantity. (netsuite.com)
- In 2021, an estimated 12.1 million Americans work in the manufacturing sector.6 (investopedia.com)
- You can multiply the result by 100 to get the total percent of monthly overhead. (investopedia.com)
- Many factories witnessed a 30% increase in output due to the shift to electric motors. (en.wikipedia.org)
External Links
How To
Six Sigma in Manufacturing:
Six Sigma is defined as "the application of statistical process control (SPC) techniques to achieve continuous improvement." Motorola's Quality Improvement Department, Tokyo, Japan, developed it in 1986. Six Sigma's core idea is to improve the quality of processes by standardizing and eliminating defects. In recent years, many companies have adopted this method because they believe there is no such thing as perfect products or services. Six Sigma aims to reduce variation in the production's mean value. This means that you can take a sample from your product and then compare its performance to the average to find out how often the process differs from the norm. If you notice a large deviation, then it is time to fix it.
Understanding the nature of variability in your business is the first step to Six Sigma. Once you've understood that, you'll want to identify sources of variation. Also, you will need to identify the sources of variation. Random variations are caused by human errors. Systematic variations can be caused by outside factors. Random variations would include, for example, the failure of some widgets to fall from the assembly line. However, if you notice that every time you assemble a widget, it always falls apart at exactly the same place, then that would be a systematic problem.
Once you identify the problem areas, it is time to create solutions. It might mean changing the way you do business or redesigning it entirely. Test them again once you've implemented the changes. If they didn't work, then you'll need to go back to the drawing board and come up with another plan.