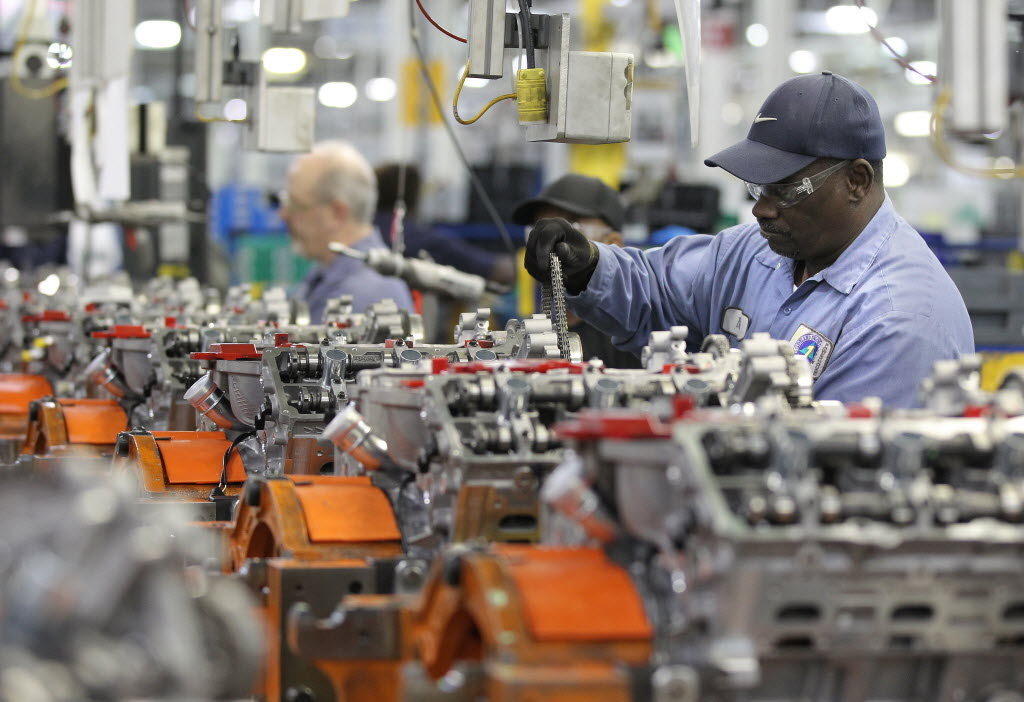
The term advanced manufacturing refers to the use of innovative technology to enhance processes and products. You can classify the technology used to achieve these results as "advanced", “innovative" or "cutting-edge". As advanced manufacturing becomes more popular, companies are incorporating new and innovative technologies to their manufacturing processes. Below are some examples of advanced manufacturing. Below are some examples of advanced manufacturing technologies.
Continuous manufacturing
Continuous manufacturing is first mentioned in the 1700s as a method of making pig iron in blast ovens. Since then, continuous manufacturing has been used in many industries including automotive, food and oil refining and chemical, as well as pulp and paper. Continuous manufacturing has captured the attention of CMOs from top pharma and other big players in the biopharmaceutical market.
The FDA and its partners recently discussed the benefits of continuous manufacturing for therapeutic proteins. This legislation would establish national standards and allow companies to create them. This legislation is intended to improve the creation and use of medical products. Further, it would also encourage companies to use continuous manufacturing to develop and improve products. It is important to make sure that continuous manufacturing is safe.
Automated processes
The benefits of automating processes in advanced manufacturing cannot be overstated. Automation can be used to make the most out of floor space, while increasing production efficiency. Manufacturing companies can increase productivity and reduce costs by collecting data and using automation technologies. Automation of the process industry can also help save time and money. Although initial investments can be costly, automation will eventually improve a company's bottom line.
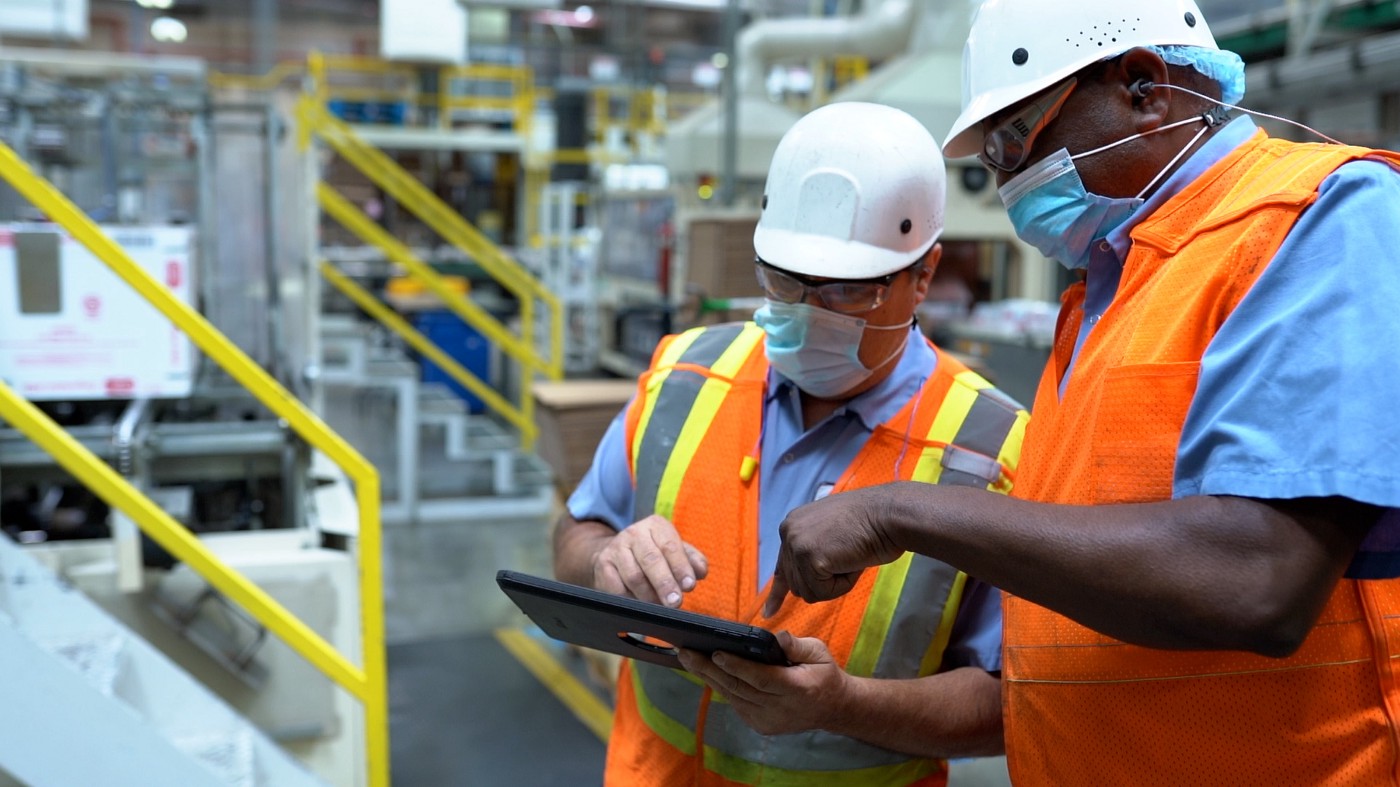
Modern companies combine advanced manufacturing processes and automated processes. Audi, for example, uses automated welding and bonding to reduce production times and save energy and weight. They also use advanced manufacturing techniques such as regenerative-braking conveyor systems. 3D printing has made the biggest leap in manufacturing, although it's been around since at least 1980s. However, this technology has only recently gained mainstream acceptance. But what makes it so attractive to manufacturers?
Internet of Things
Manufacturing is being transformed by the IIoT revolution. This revolution uses sensors to monitor machinery and processes. These sensors collect data in different areas of the manufacturing process to feed into a central hub. This data can then be analyzed to help optimize processes and eliminate waste. Advanced manufacturers have already begun to use IIoT sensors in order to optimize production processes. The IIoT is an industrial version of key fobs.
To deploy IIoT effectively and efficiently, you need a roadmap and the development capabilities to create use cases. Three waves of deployment are shown in the following roadmap from an automaker:
Cost-effectiveness
It is not always possible to compare the costs of advanced manufacturing with traditional production methods. Instead, traditional cost-benefit analyses are not enough to determine economic benefits. However, a holistic model that considers both costs and benefits of technology can help to identify new benefits and accelerate decision-making processes. Munker and Schroer develop a cost-benefit tool to address the main issues involved in AMS implementation.
Information technology is rapidly changing the face and cost of manufacturing. As production systems become more networked and smart, they are also becoming more efficient. Cost pressure has increased the importance of productivity and responding to customer needs. The adoption of modern manufacturing technologies will accelerate the development of new technologies and increase their cost-effectiveness. As the industry digitizes, so will the adoption of these technologies.
Human error reduction
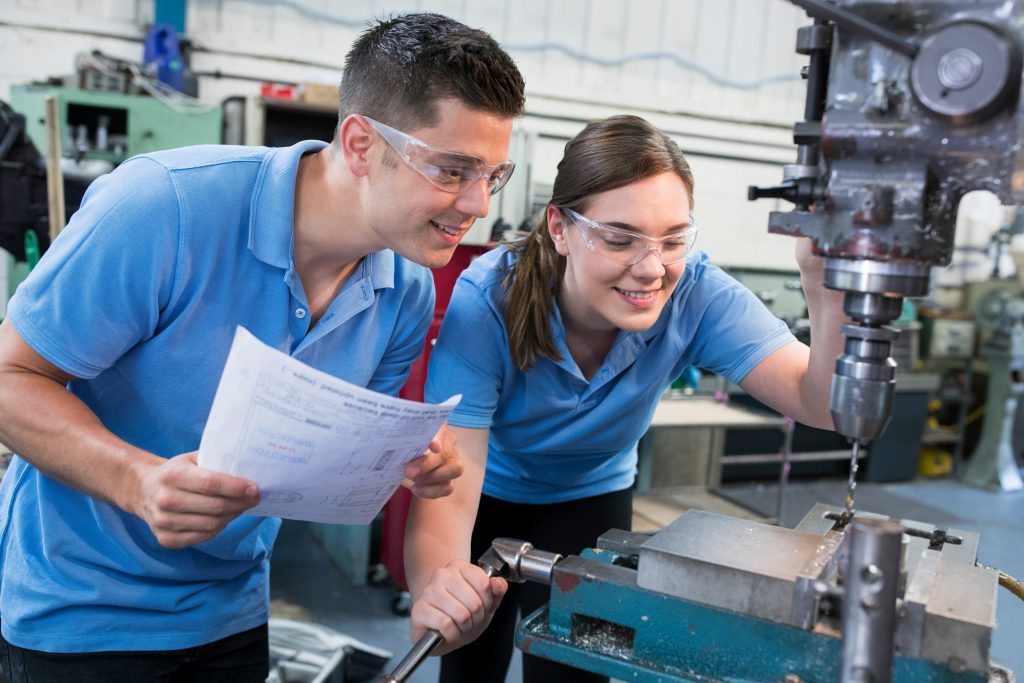
Humans make mistakes. However, the process that is used to make a product usually protects it. Human error may occur when employees do not follow the instructions or fail in writing. When they make drugs, pharmaceutical laboratories for example must follow certain procedures. Some employees believe they are familiar with a process and know how to use the correct ingredients. They then proceed to make the compound without consulting the written instructions.
A way to reduce human errors is to communicate effectively between junior and senior employees. People will make mistakes if they are treated badly. Managers must not punish employees for asking questions. Employees should feel comfortable asking question and will not hesitate to ask for clarification if they are uncomfortable. Respect senior employees' opinions and communicate with them in a friendly and professional manner.
FAQ
What is the importance of automation in manufacturing?
Not only is automation important for manufacturers, but it's also vital for service providers. It allows them provide faster and more efficient services. It helps them to lower costs by reducing human errors, and improving productivity.
What is the role of a manager in manufacturing?
Manufacturing managers must ensure that manufacturing processes are efficient, effective, and cost-effective. They should be alert for any potential problems in the company and react accordingly.
They should also learn how to communicate effectively with other departments, including sales and marketing.
They should also be aware of the latest trends in their industry and be able to use this information to help improve productivity and efficiency.
How does a production planner differ from a project manager?
The main difference between a production planner and a project manager is that a project manager is usually the person who plans and organizes the entire project, whereas a production planner is mainly involved in the planning stage of the project.
Statistics
- (2:04) MTO is a production technique wherein products are customized according to customer specifications, and production only starts after an order is received. (oracle.com)
- [54][55] These are the top 50 countries by the total value of manufacturing output in US dollars for its noted year according to World Bank.[56] (en.wikipedia.org)
- You can multiply the result by 100 to get the total percent of monthly overhead. (investopedia.com)
- It's estimated that 10.8% of the U.S. GDP in 2020 was contributed to manufacturing. (investopedia.com)
- In 2021, an estimated 12.1 million Americans work in the manufacturing sector.6 (investopedia.com)
External Links
How To
Six Sigma and Manufacturing
Six Sigma is "the application statistical process control (SPC), techniques for continuous improvement." Motorola's Quality Improvement Department in Tokyo, Japan developed Six Sigma in 1986. Six Sigma is a method to improve quality through standardization and elimination of defects. Many companies have adopted this method in recent years. They believe there is no such thing a perfect product or service. The main goal of Six Sigma is to reduce variation from the mean value of production. It is possible to measure the performance of your product against an average and find the percentage of time that it differs from the norm. If the deviation is excessive, it's likely that something needs to be fixed.
The first step toward implementing Six Sigma is understanding how variability works in your business. Once you have this understanding, you will need to identify sources and causes of variation. You'll also want to determine whether these variations are random or systematic. Random variations happen when people make errors; systematic variations are caused externally. If you make widgets and some of them end up on the assembly line, then those are considered random variations. But if you notice that every widget you make falls apart at the exact same place each time, this would indicate that there is a problem.
Once you have identified the problem, you can design solutions. You might need to change the way you work or completely redesign the process. Once you have implemented the changes, it is important to test them again to ensure they work. If they didn't work, then you'll need to go back to the drawing board and come up with another plan.